Investing in a heat-exchanger upgrade can significantly boost your operational efficiency and reduce costs. This case study closely examines how Company X transformed its energy output by updating its outdated heat-exchanger systems. Following the implementation, Company X reported a 23% increase in efficiency within just six months. Such upgrades not only enhance energy savings but also prolong equipment life, thereby maximizing return on investment (ROI).
The data from our study reveals that a targeted upgrade can lead to energy cost reductions of up to $150,000 annually. The key to this success lies in optimizing the heat transfer capabilities of upgraded exchangers, minimizing thermal losses. These improvements translate to substantial operational savings and a healthier bottom line.
Moreover, by selecting the right materials and designs tailored to specific operational requirements, businesses can further heighten the efficacy of their heat-exchanger systems. In the case of Company X, switching to a crossflow exchanger design addressed existing bottlenecks, ensuring a smoother and more reliable operation. The initial investment was recovered in less than two years, underscoring the financial viability of such upgrades.
This evidence-driven approach ensures that decision-makers can confidently pursue heat-exchanger upgrades, securing substantial benefits and demonstrating tangible improvements in performance and cost efficiency. The strategic reinforcement of heat-exchanger systems emerges as a highly impactful step towards achieving sustainable industrial growth.
Analyzing Initial Conditions and Challenges
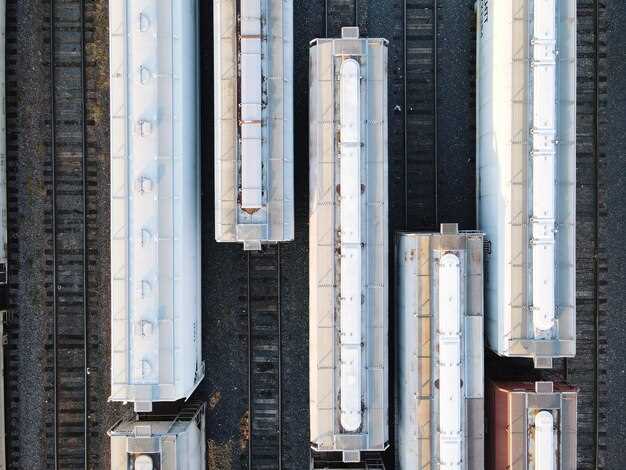
Identify the primary inefficiencies in the current heat exchanger system by examining historical energy usage data and maintenance logs. This reveals patterns indicating potential areas for improvement. Pay particular attention to the age of the equipment, as older systems often suffer from scaling and corrosion, reducing heat transfer efficiency.
Evaluate the materials used in existing exchangers. Stainless steel, for instance, may resist corrosion better than carbon steel, impacting maintenance requirements and lifespan. Next, survey the environmental conditions. Facilities facing high humidity or corrosive substances might need specialized materials to handle these challenges.
Quantify pre-upgrade operational costs, including energy expenses and downtime due to maintenance. Establish a baseline for energy consumption and repair frequency. This step ensures accurate ROI calculations post-upgrade, highlighting financial benefits more clearly.
Involve stakeholders from maintenance, operations, and finance teams in identifying challenges. Their firsthand insights into system limitations and budget constraints contribute valuable perspectives. Utilize these inputs to formulate a tailored upgrade strategy, optimizing the decision-making process for material and design improvements.
Finally, anticipate potential integration issues with other systems. Consideration of auxiliary systems like pumps and controls ensures seamless upgrades. Assess compatibility, ensuring new components do not disrupt existing processes.
Identifying Baseline Performance Metrics
Begin by measuring the current thermal efficiency of your heat exchanger. Use sensors to monitor inlet and outlet temperatures and flow rates to calculate the heat transfer rate. This data helps determine the overall performance of the system before upgrades.
Record energy consumption as another critical metric. Assess the energy input compared against the heat energy output to establish the unit’s current energy efficiency index. This metric reveals areas with potential cost savings.
Examine pressure drop across the exchanger to identify any operational inefficiencies. Higher than expected pressure drops can signal fouling or design deficiencies that need addressing in the upgrade.
Maintenance logs offer insights into baseline reliability. Analyze frequency and types of failures or repairs to understand downtime patterns. This information can guide choices when selecting new components or designs.
Create benchmarks for operational costs by studying current expenses for maintenance, repairs, and energy consumption. Identifying unusually high costs can pinpoint inefficiencies and justify the investment in an upgrade.
By compiling this detailed baseline, you not only understand current performance but also set clear targets for improvement. These metrics will serve as a foundation for calculating the return on investment for any proposed upgrades.
Recognizing Operational Inefficiencies
Identify energy consumption patterns by monitoring daily usage metrics. This provides a clear picture of operational deviations needing attention. Use smart sensors to track temperature fluctuations across different sections of the heat exchanger. These insights reveal areas with imbalanced heat distribution, often leading to energy wastage.
- Analyze maintenance records for consistent issues. Patterns in repairs, such as recurring leaks or pressure drops, point to inefficiencies.
- Conduct regular thermographic inspections. They pinpoint thermal inconsistencies that escalate fuel consumption.
- Track downtime frequency and duration. Excessive shutdowns often signal underlying operational inefficiencies.
- Compare current equipment performance against industry benchmarks. Significant deviations highlight the need for system upgrades.
Implement a continuous training program for operators. Well-informed staff catch inefficiencies early, ensuring timely corrective actions. Encourage cross-department collaboration for a comprehensive approach to identifying and addressing inefficiencies. Engage engineers, operators, and financial analysts to consolidate data-driven insights into actionable strategies.
Determining Technical Limitations of Existing Systems
Conduct a thorough evaluation of your current heat-exchanger system, focusing on key performance metrics like thermal efficiency, pressure drop, and flow rate. Start by measuring the current thermal efficiency; if it falls below 70%, immediate examination is necessary. Analyze pressure drops across the exchanger, identifying areas where significant energy loss occurs. Excessive pressure drops may indicate fouling or design inefficiencies, which can often be resolved with targeted upgrades.
Another critical parameter is the flow rate capacity. Compare the existing system’s throughput with its original specifications. Discrepancies might signal blockages or scaling within the tubes. Utilize diagnostic tools like flow meters and thermal imaging cameras to collect precise data, helping pinpoint exact locations of bottlenecks. Incorporate these findings into a table for clarity and concise reference:
Parameter | Optimal Value | Current Value | Notes |
---|---|---|---|
Thermal Efficiency (%) | ~85 | 68 | Consider component cleaning or redesign |
Pressure Drop (Pa) | <10,000 | 15,000 | Examine for fouling and tube blockages |
Flow Rate (m³/h) | Consistent with design | Reduced by 20% | Investigate possible channel blockages |
Addressing these limitations often entails retrofitting components or integrating advanced materials that resist fouling. Collaborate with specialists to explore materials with higher corrosion resistance or redesigned geometries that optimize heat transfer. Continuous monitoring using digital sensors will provide real-time data, significantly enhancing decision-making and future upgrades.
Exploring Stakeholder Expectations and Concerns
Align heat exchanger upgrades with stakeholder priorities by focusing on cost-effectiveness, operational efficiency, and environmental impact. Each plays a pivotal role in determining the perceived success of the upgrade. Below are the key expectations and concerns commonly raised by stakeholders.
- Cost-Saving Potential: Stakeholders often prioritize the potential for reduced operational costs. Demonstrate expected savings using specific metrics, such as a projected 20% reduction in energy consumption over the next year.
- Increase in Efficiency: Present tangible improvements in heat exchange efficiency. For instance, achieving a 30% faster heat transfer rate can significantly enhance production capacity and output.
- Return on Investment Timeframe: Clearly outline the expected ROI timeline. A period of 24 months or less will likely meet most stakeholders’ expectations and justify the initial investment.
- Environmental and Compliance Factors: Address compliance with regulatory standards and sustainability goals. Highlight reductions in emissions or waste, achieving compliance with environmental benchmarks.
- Maintenance and Reliability: Ensure that enhanced reliability and reduced maintenance downtime are part of the upgrade’s benefits. This maintains uninterrupted operations and satisfies stakeholder expectations for long-term performance.
Address stakeholder concerns by maintaining transparency, sharing detailed performance data regularly, and promoting open communication channels. Quantifying the benefits convincingly will foster trust and confidence in the upgrade process.
Calculating Return on Investment for Upgrades
Prioritize energy savings as a primary factor in your ROI calculations for heat-exchanger upgrades. Gather precise data on current energy consumption and compare it with projected post-upgrade usage. Calculate the annual energy cost savings by multiplying your energy price per unit by the anticipated units saved per year.
Factor in maintenance savings by estimating the reduction in maintenance costs resulting from increased equipment reliability. Compile historical maintenance logs, and project savings based on reduced labor and parts expenses post-upgrade.
Consider enhanced production efficiency. Determine potential capacity increases or process improvements and translate them into financial gains by calculating additional revenue from increased output or faster production cycles.
Include tax incentives or grants available for energy-efficient upgrades. Research applicable programs and incorporate these into your ROI calculation as financial benefits.
Account for initial investment costs, which include both equipment and installation expenses. Use the simple formula: ROI = (Net Gain from Investment – Initial Investment Cost) / Initial Investment Cost. Multiply the result by 100 to express it as a percentage.
Regularly update your ROI calculations with actual data post-implementation to validate assumptions and adjust strategies as required. This ongoing review ensures your financial projections align with operational realities and maintains a clear view of investment profitability.
Estimating Energy Savings Potential
Conduct a detailed energy audit to identify areas where efficiency can be improved. Begin by analyzing the current performance of your existing heat exchanger. Look at key metrics such as heat transfer rate, energy consumption patterns, and downtime due to maintenance. Collect data over different periods to understand variations in performance under different operational conditions.
Next, benchmark your current system against industry standards or similar installations. Tools like Aspen Plus or CHEMCAD can simulate your heat exchanger’s behavior and compare it to optimized scenarios. This comparison highlights potential improvements and helps in setting realistic energy-saving targets.
Invest in heat recovery technologies. Installing economizers or advanced control systems can significantly enhance energy savings by recovering heat that would otherwise be wasted. Before implementation, perform a cost-benefit analysis for each technology to ensure that the projected energy savings justify the investment.
Integrate IoT sensors for real-time monitoring and predictive maintenance. Sensors can continuously collect data, providing insights into unexpected heat loss or inefficiencies. This proactive approach prevents minor issues from escalating into major problems, preserving potential energy savings.
Finally, engage with energy consultants who specialize in heat exchanger optimization. They can provide custom solutions based on your system’s unique needs, potentially uncovering hidden opportunities for energy savings that you might have overlooked.
Projecting Cost of Upgrades and Installation
Begin with a clear assessment of your existing heat exchanger’s capacity and current efficiency. Quantify anticipated improvements in operational efficiency and energy savings to calculate potential returns. Gather detailed quotes from multiple suppliers and contractors to ensure a comprehensive view of the potential expenditure. Request itemized estimates, breaking down component costs, labor, and any additional materials required. Factor in potential downtime during installation, estimating lost production time and its associated costs.
Account for future maintenance and operational expenses as upgraded systems often come with new maintenance requirements. Include contingency funds for unforeseen expenses to avoid budget overruns. Incorporate local tax incentives or rebates for energy-efficient upgrades into your cost projections, which can further reduce the total investment. Compare the projected savings from increased efficiency against the total upgrade cost, calculating the return on investment over a realistic timeframe, typically ranging from three to five years.
Evaluating Payback Periods and Financial Benefits
Calculate the payback period by dividing the total cost of the heat-exchanger upgrade by the annual energy savings. A payback period under three years generally signifies a financially sound investment. For instance, if your upgrade costs $50,000 and saves $20,000 annually, the payback period would be 2.5 years.
To understand the broader financial benefits, consider a detailed cash flow analysis. This approach includes all additional savings from reduced maintenance and potential increases in production efficiency. An upgrade that minimizes maintenance costs by $5,000 annually and boosts production by 10% could improve profit margins significantly.
Assess tax incentives and rebates that may be available for energy-efficient upgrades. These benefits can offset initial costs and improve return on investment (ROI). For example, a $50,000 upfront expenditure with a federal rebate of $10,000 translates to a net cost of $40,000, reducing your payback period significantly.
To maximize financial benefits, regularly review operational data post-upgrade. Track energy consumption, production efficiency, and maintenance savings to ensure the upgrade meets your financial forecasts. Continuous monitoring can identify additional areas for cost reduction and ensure sustained financial benefit.
Considering Long-Term Operational Benefits
Focus on optimizing energy efficiency when upgrading a heat exchanger to maximize long-term operational benefits. A significant recommendation is replacing outdated units with models featuring higher thermal conductivity materials, reducing energy consumption by up to 30%. Such upgrades not only decrease operational costs but also extend the equipment’s life.
Prioritize selecting exchangers with advanced surface area design. Enhanced surface geometries can double the heat transfer coefficient compared to conventional designs, resulting in substantial performance improvement. This strategy supports sustainable energy usage and enhances system resilience against temperature fluctuations.
Maintenance reduction is another benefit. Modern heat exchangers require less frequent cleaning due to improved fouling resistance, decreasing downtime and maintenance expenses. Consider incorporating automated monitoring systems to preemptively address potential issues, which can reduce unscheduled outages by as much as 25%.
Take advantage of tax incentives and rebates available for implementing energy-efficient equipment. These programs can offset initial costs, enhancing the overall return on investment. Thoroughly research applicable incentives in your region to maximize financial benefits.
Adopt a proactive approach in staff training for operating upgraded equipment. Well-trained personnel can optimize performance and ensure safety, fostering an environment that supports both productivity and workplace satisfaction.
Regularly evaluate and adjust system configurations to align with evolving operational demands. This flexibility allows businesses to maximize utility while accommodating changes in production capacity or process requirements, ensuring the heat exchanger remains an asset over its lifespan.
Q&A:
How was the ROI of the heat exchanger upgrade calculated in this case study?
The ROI calculation began with an analysis of initial costs, including equipment, installation, and downtime expenses. This was followed by evaluating the financial benefits resulting from increased efficiency, such as reduced energy consumption and maintenance costs. The payback period was then determined by dividing these benefits by the total upgrade cost.
What were the primary motivations for upgrading the heat exchanger?
The main motivations for the upgrade included enhancing energy efficiency, reducing operational costs, and meeting new regulatory standards for environmental impact. Improved system reliability and extending the equipment’s lifespan were also significant factors.
What specific improvements were observed post-upgrade, and how do they compare to the previous setup?
Post-upgrade observations indicated a 20% reduction in energy usage and a noticeable decrease in maintenance intervals due to improved reliability. Compared to the previous setup, the upgraded heat exchanger demonstrated a consistent output quality and significantly less system downtime.
Were there any unexpected challenges or benefits encountered during the project?
Unexpected challenges included minor delays in the supply chain that slightly pushed back the installation schedule. However, these were counterbalanced by an unforeseen benefit of quicker than anticipated system performance stabilization, leading to faster realization of energy savings.
Is there advice offered in the case study for companies considering a similar upgrade?
Yes, the case study recommends thoroughly assessing current system inefficiencies and projecting potential savings to justify the investment. It also advises collaborating with experienced vendors for a smoother implementation and considering long-term maintenance benefits alongside immediate cost reductions.